ABSTRACT
QPad (QuasiPad) is a novel technique to produce flexible, foam-like material from traditional thermoplastics. While the main goal of infill is to provide structural strength and rigidity to 3D printed objects, achieving softness and flexibility remains a significant challenge. This challenge arises from the inherent hardness of materials used in fused deposition modeling (FDM) technology. Options such as infill type and density can be adjusted, but these often compromise the internal structural integrity or the object’s ability to absorb impact and recover its shape.
This paper explores how optimizing four key parameters—(1) infill type, (2) infill density, (3) perimeter width, and (4) extrusion multiplier—enables the use of standard materials, such as PLA, to design flexible objects. This approach avoids the need for material changes, streamlining the design and manufacturing process while maintaining flexibility and shock-absorption capabilities.
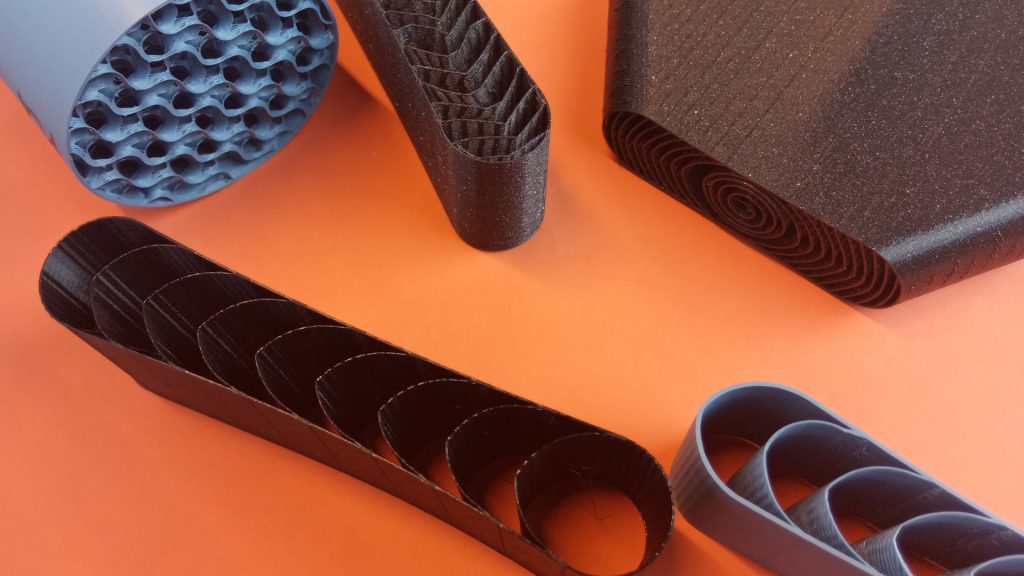
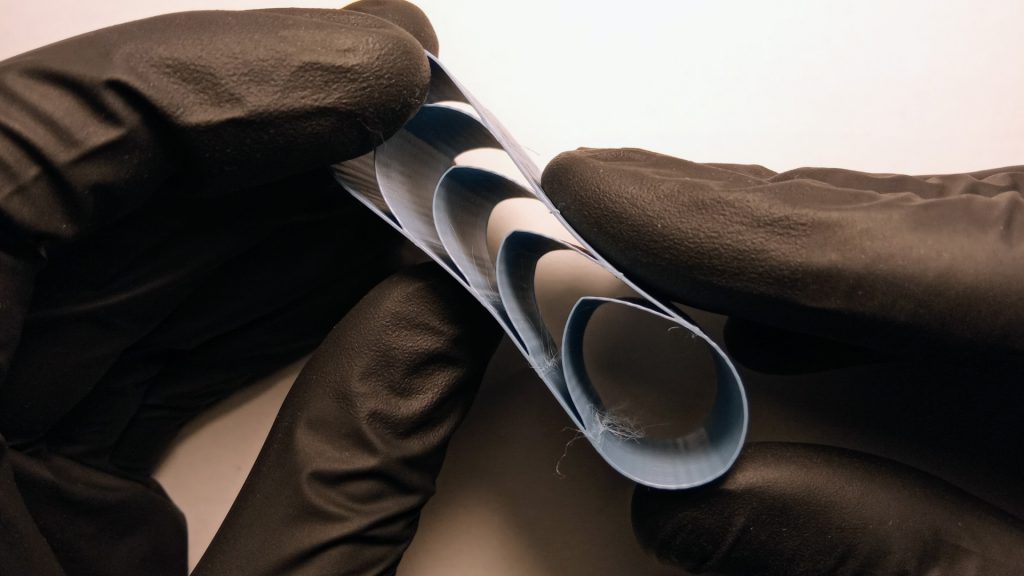
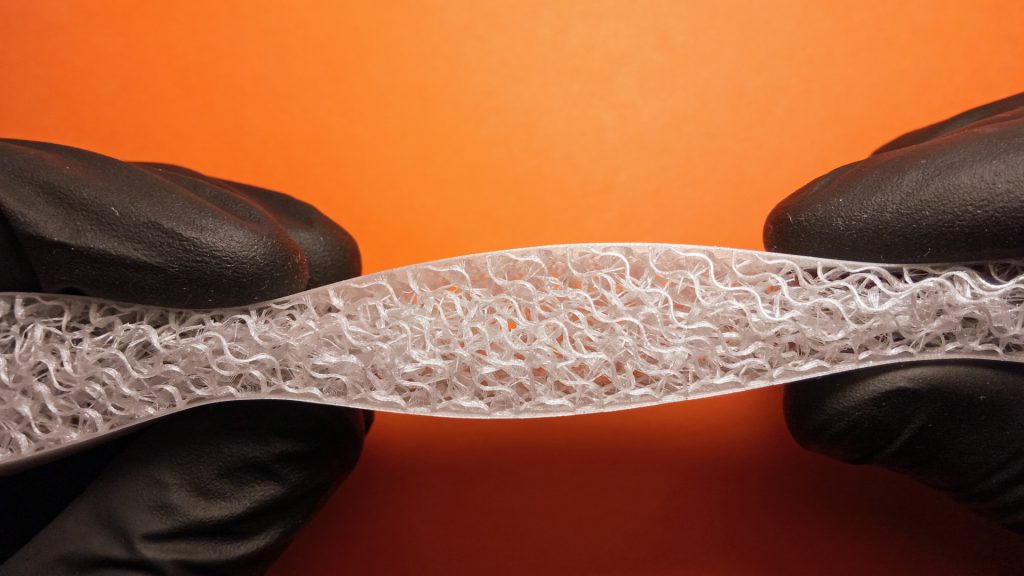
CCS CONCEPTS
- Human-centered computing → Human computer interaction (HCI); Human-centered computing;
KEYWORDS
3D printing, memory, absorbing, material, foam.
INTRODUCTION
In FDM, complex geometries rely on external perimeters to define the shape and appearance of an object. At the same time, the infill contributes to its structural integrity and supports the uppermost surfaces. The type of printing filament also affects strength and flexibility. However, achieving the desired specifications often requires compromises.
In contrast, QPad is engineered using traditional materials, even though these materials often fail to provide the necessary features. The primary limitation of such materials is their stiffness; however, this becomes a feature that enables an object to recover its shape after deformation. Object perimeters are used as a shape recovery mechanism, while infill plays a crucial role in absorbing the impact. By fine-tuning the four parameters mentioned earlier, we have achieved a unique combination of softness, resistance to deformation, and shape recovery properties.
QPad shape can be designed in the computer aided design (CAD) software, or basic shapes in the slicing software (slicers) can be used, for example, cylindrical. As the object perimeter is responsible for recovering its shape, the primary setting used for this is the number of perimeters and their extrusion width. On the other hand, as the infill resists the applied force thus its type, density, and extrusion multiplier are the main factors that impact its resistance. When the cylinder is printed, we have a “non-functioning” solid object because the infill layers are bonded together. The material will only start to ‘work’ when it is ‘broken’, i.e. an initial deformation is applied, after which some of the layers loosen, allowing it to move and ‘work’ freely. The initial deformation is carried out by compressing the material evenly on both sides. The more it is compressed, the freer it will move and the less resistance it will have.
QPad presents the following contributions:
- Provides a detailed analysis of the behavior and durability of thermoplastic-based foams.
- Offers fast and accessible workflows for 3D printing flexible objects of any size, shape and thickness.
- Presents several types of mechanical designs 3D printed from different materials.
- Conducts an extensive study of mechanical properties and compares various designs.
STAY TUNED!
More information will be posted soon.
Please check back later for updates.
Creative Commons
Attribution-NonCommercial-NoDerivatives 4.0 International