VIDEO MATERIALS | PROJECT FILES | CONTRIBUTE | COLLABORATE
ABSTRACT
We demonstrate a new approach, QWeave (QuasiWeave), for 3D printing “zero-layer” woven fabric that is more durable and flexible than previous efforts. Previous attempts to create woven-like fabrics with fused deposition modeling (FDM) printers failed due to challenges such as poor bending angles, weak adhesion between layers, and lack of material variety. These issues rendered them unsuitable for practical applications.
This study addresses these challenges by demonstrating advanced manufacturing workflows: (1) 3D printing in a zig-zag pattern, (2) weaving, (3) pressing, and (4) snapping. Beyond mimicking traditional textiles, this workflow offers new insights into the behavior of thermoplastic-based materials, enabling the development of customizable and adaptable fabrics from a diverse range of materials, tailored to individual preferences and applications.
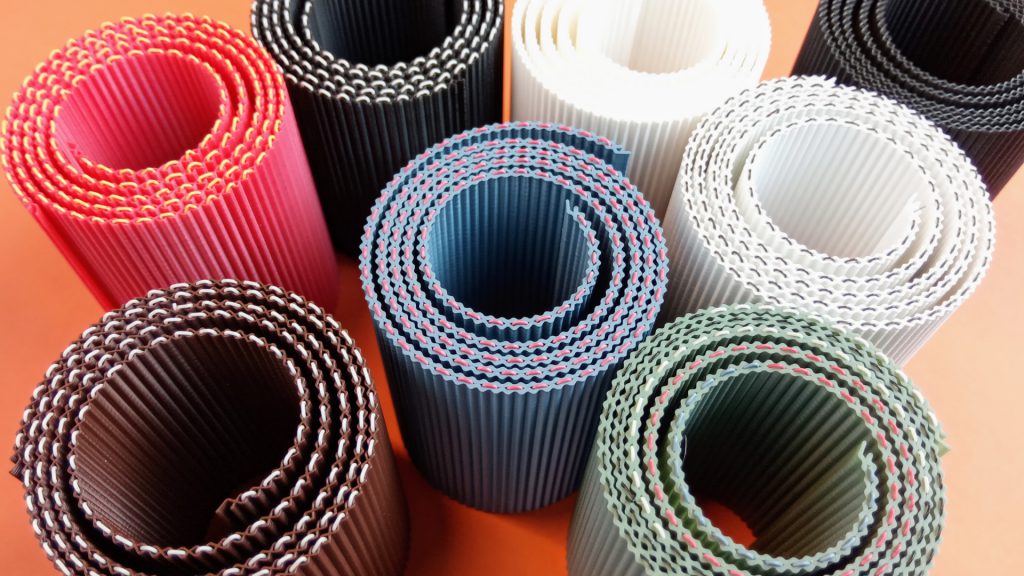
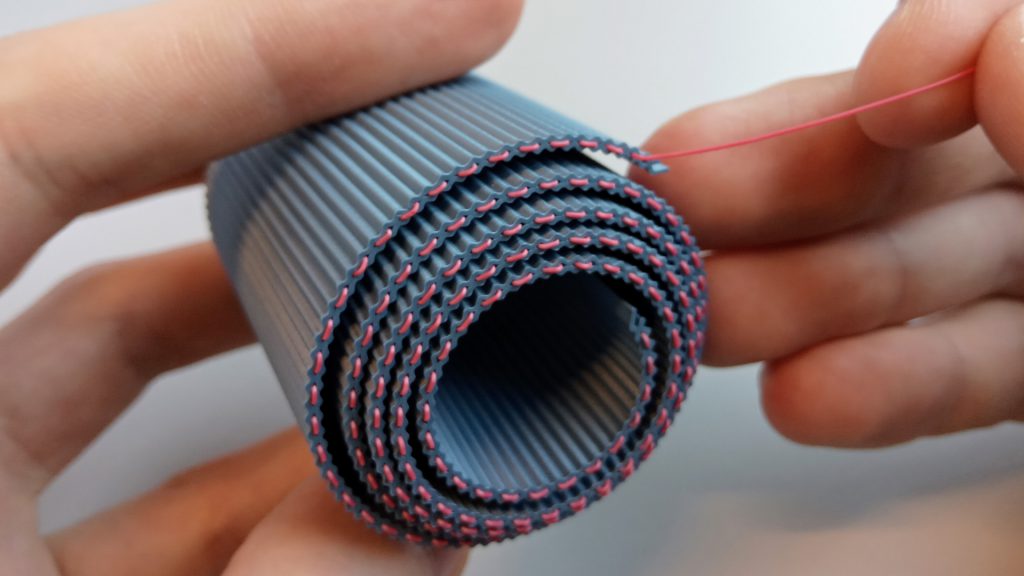
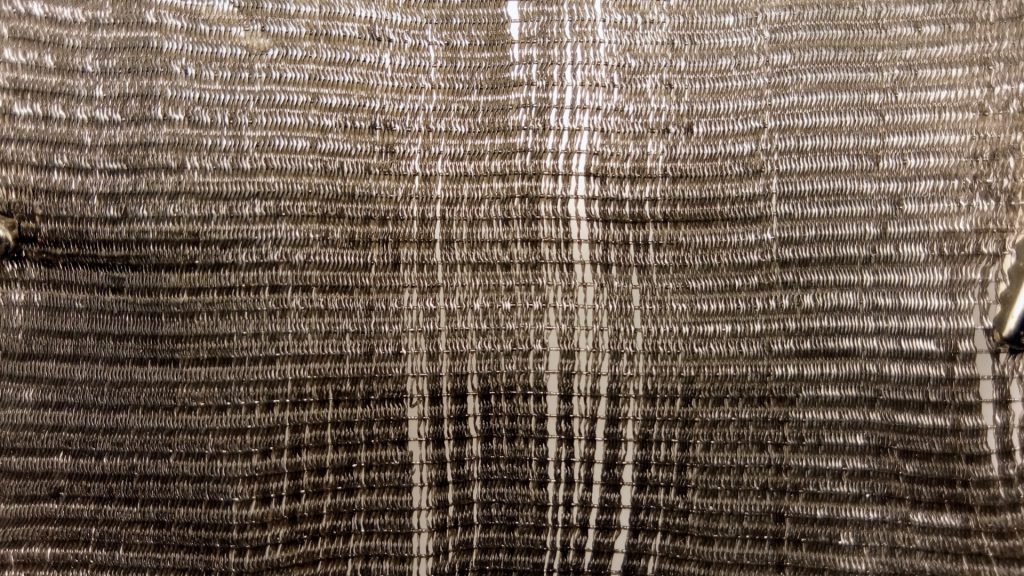
CCS CONCEPTS
- Human-centered computing → Human computer interaction (HCI); Human-centered computing;
KEYWORDS
3D printing, fabrics, textiles.
INTRODUCTION
The field of 3D printing is expanding beyond its initial applications in prototyping and manufacturing to areas such as textiles and fabrics. Traditional textile manufacturing relies on techniques like weaving and knitting. However, reproducing these techniques with FDM technology has proven challenging. These challenges arise from the technology itself, which relies on the deposition of hot, liquid material on a planar surface layer by layer. Therefore, most efforts to create 3D-printed fabrics have been limited by issues like poor flexibility, cracking between layers, and a lack of structural integrity.
The idea of ‘zero-layer’ fabric aims to overcome these limitations by using poor layer adhesion—a common cause of print failure—as a method to manufacture fabric warp. This approach further improves durability by weaving the weft. By employing techniques such as printing in a zig-zag pattern, weaving, pressing, and snapping, we have developed a cost-effective and scalable method to produce thermoplastic-based textiles that behave much like their traditionally woven counterparts but can change their features depending on the context and materials used.
The zig-zag pattern, designed in computer-aided design (CAD) software, acts as the fabric warp and is printed using a single or multi-material setup. After the required amount of material is extruded, this plastic thread is used as a weft during the weaving process. The finished fabric is stiff and thick, requiring flattening with a press. Since the layers are still connected, they need to be broken apart by snapping. Our workflow indicates the ability to customize a fabric at any point in the manufacturing process, whether it be its shape, length, height, thickness, or even materials used for warp and weft.
QWeave presents the following contributions:
- Provides a detailed analysis of the behavior and durability of thermoplastic-based woven fabrics.
- Presents versatile and accessible workflows for 3D printing fabrics of any size, shape, thickness and material.
- Multi-material options for warp and weft that further enhance fabric features.
- Includes a study of the mechanical properties of fabrics combining various materials.
- Describes multiple post-processing techniques such as sewing, heat-bonding, annealing and de-pleating.
STAY TUNED!
More information will be posted soon.
Please check back later for updates.
Creative Commons
Attribution-NonCommercial-NoDerivatives 4.0 International